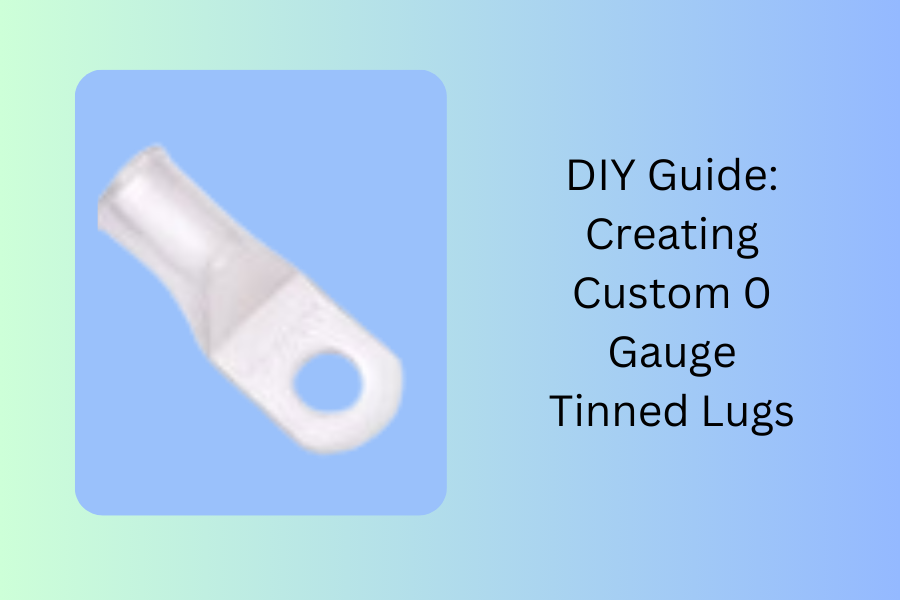
If you’re working on a project that involves heavy-duty electrical wiring, you may need to use 0 gauge tinned lugs. These are essential components for ensuring a secure and reliable connection in high-current applications. While you can buy pre-made lugs, creating your own custom 0 gauge tinned lugs can save money and provide a more tailored solution for your specific needs. This DIY guide will walk you through the process step-by-step, from gathering materials to the final installation.
Materials and Tools Needed
Before you begin, gather the following materials and tools:
Materials
- 0 Gauge Cable: The specific length you need for your project.
- Copper Lugs: Ensure they are rated for 0 gauge wire.
- Flux: A good quality flux helps with the tinning process.
- Solder: Use high-quality, lead-free solder.
- Heat Shrink Tubing: Choose a size that fits snugly over the lug and wire.
- Tinning Powder: This will make the tinning process easier and more efficient.
Tools
- Wire Strippers: For stripping the insulation from the wire.
- Crimping Tool: Specifically rated for 0 gauge cable lugs.
- Soldering Iron: With sufficient wattage to handle heavy gauge wire.
- Heat Gun: For shrinking the tubing.
- Vise: To hold the wire and lug steady while working.
- Gloves and Safety Glasses: For protection while working.
Step-by-Step Guide
Step 1: Preparing the Cable
Start by cutting your 0 gauge cable to the desired length. Once cut, use wire strippers to remove about 1 inch of insulation from the end of the cable. Be careful not to nick the copper strands as this can weaken the connection.
Step 2: Applying Flux
Dip the stripped end of the cable into flux. The flux helps to clean the metal and improve the flow of solder during the tinning process. Make sure the copper strands are thoroughly coated with flux.
Step 3: Tinning the Cable
Place the cable end into a vise to hold it steady. Heat up your soldering iron and apply solder to the copper strands. Allow the solder to flow into the strands, ensuring they are completely coated. This process is called tinning and it prepares the wire for crimping and improves the electrical connection.
Step 4: Inserting the Cable into the Lug
Once the cable end is tinned, insert it into the copper lug. Make sure it fits snugly and that all the strands are inside the lug.
Step 5: Crimping the Lug
Use a crimping tool rated for 1/0 awg tinned copper lugs to crimp the lug onto the cable. Position the lug in the crimping tool and apply firm, even pressure. Proper crimping is crucial for a strong and reliable connection, so ensure the lug is securely attached to the cable.
Step 6: Soldering the Lug
To further secure the connection, you can solder the lug to the cable. Heat the lug with your soldering iron and apply solder until it flows into the lug and around the cable strands. Be careful not to overheat the lug, as this can damage the cable insulation.
Step 7: Applying Heat Shrink Tubing
Slide a piece of heat shrink tubing over the lug and cable connection. Use a heat gun to shrink the tubing until it fits snugly around the lug and cable, providing insulation and strain relief. Make sure the tubing covers the entire connection point.
Step 8: Inspecting the Connection
After the heat shrink tubing has cooled, inspect your work. Ensure the lug is securely crimped and soldered to the cable, and that the heat shrink tubing is properly applied. Tug lightly on the cable to verify that the connection is strong.
Tips for Success
- Use Quality Materials: High-quality copper lugs and solder will ensure a better connection.
- Practice Safety: Always wear gloves and safety glasses when working with solder and heat.
- Proper Tool Use: Ensure your crimping tool and soldering iron are rated for the gauge of wire you are working with.
- Double Check Connections: Before finalizing your project, double-check all connections for security and reliability.
Conclusion
Creating custom 1/0 awg tinned copper lugs may seem daunting at first, but with the right materials, tools, and a bit of patience, it can be a straightforward process. This DIY guide provides all the steps necessary to make your own high-quality lugs, ensuring your electrical connections are robust and reliable. Whether you’re working on an automotive project, a high-power audio system, or another application requiring heavy-duty wiring, custom tinned lugs can offer a tailored solution that meets your specific needs. Happy wiring!