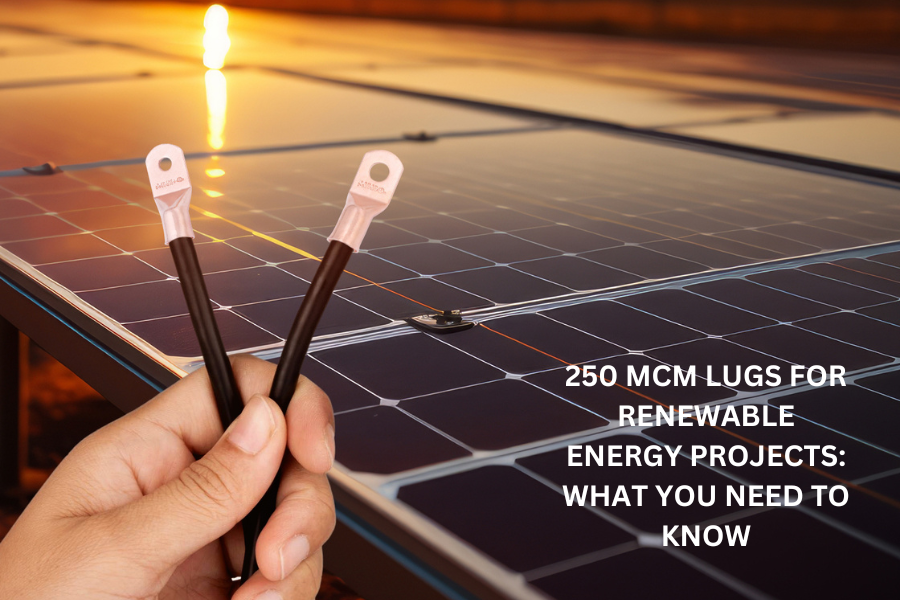
In the ever-evolving landscape of renewable energy, the efficient and reliable transmission of electricity is paramount. A critical component in this infrastructure is the lug, a specialized connector used to terminate electrical conductors. Among these, 250 MCM lugs play a pivotal role in accommodating the high current capacities required for large-scale renewable energy projects, such as solar farms and wind power plants.
The 250 MCM lug, a specialized connector used to terminate electrical conductors, is designed to handle the high current capacities required for large-scale renewable energy projects. Its robust construction and ample cross-sectional area enable it to efficiently and reliably transmit electricity, ensuring the smooth operation of solar farms, wind power plants, and other renewable energy installations.
These lugs are typically made of high-quality materials, such as copper or aluminum, and are designed to withstand the rigors of outdoor environments, including exposure to extreme temperatures, humidity, and ultraviolet radiation. They are also available in various styles, including compression, split-barrel, and solderless, to accommodate different installation requirements and conductor types.
Understanding 250 MCM Lugs
MCM, or thousands of circular mils, is a unit used to measure the cross-sectional area of a conductor. A 250 MCM lug is designed to accommodate a conductor with a cross-sectional area of 250,000 circular mils. This substantial size enables it to handle significant electrical currents without overheating or experiencing excessive voltage drop.
The choice of 250 MCM lug is influenced by several factors, including the conductor material, lug style, insulation requirements, termination method, and environmental conditions. Careful consideration of these factors is essential to ensure the optimal performance and reliability of the electrical connections in renewable energy projects.
Key Applications in Renewable Energy Projects
● Solar Farms: Solar panels generate DC electricity, which is then converted to AC for grid integration. 250 MCM lugs are used to connect the output of solar inverters to the main grid connection point, ensuring efficient power transfer.
● Wind Power Plants: Wind turbines produce AC electricity that is collected and fed into the grid. 250 MCM lugs are employed to connect the output of wind turbines to the substation or collection point.
● Battery Energy Storage Systems (BESS): BESS are becoming increasingly important for grid stability and peak load management. 250 MCM lugs are used to connect the batteries to the grid or other electrical components, ensuring reliable power flow.
Factors to Consider When Selecting 250 MCM Lugs
● Conductor Material: The lug should be compatible with the conductor material being used (e.g., copper, aluminum).
● Lug Style: There are various lug styles available, including compression, split-barrel, and solderless. The choice depends on the specific application and installation requirements.
● Insulation: The lug may require insulation to prevent electrical short circuits or contact with other components.
● Termination Method: Consider the termination method (e.g., crimping, bolting) that will be used to connect the conductor to the lug.
● Environmental Factors: The lug should be suitable for the environmental conditions where it will be installed. This includes:
- Temperature: The lug must be able to withstand both high and low temperatures without compromising its performance or durability. Extreme temperatures can cause materials to expand or contract, potentially leading to loose connections or mechanical failure.
- Humidity: High humidity can accelerate corrosion and create favorable conditions for mold growth. Lugs used in humid environments should be made of materials that are resistant to moisture and corrosion.
- Corrosion: Exposure to corrosive substances, such as saltwater or industrial pollutants, can degrade the lug’s material and weaken its structural integrity. Lugs used in corrosive environments should be made of materials that are resistant to corrosion, such as stainless steel or copper alloy.
- Ultraviolet (UV) Radiation: Exposure to UV radiation can cause the insulation of the lug to degrade, increasing the risk of electrical short circuits or other hazards. Lugs used in outdoor environments should have UV-resistant insulation.
- Mechanical Stress: Lugs may be subjected to mechanical stress due to vibrations, wind loading, or other factors. The lug should be designed to withstand these forces without experiencing deformation or failure.
Installation and Maintenance
Proper installation of 250 MCM Cable Lugs is crucial to ensure reliable electrical connections. Adhering to the manufacturer’s guidelines and using appropriate tools is essential. This includes selecting the correct lug style, preparing the conductor for termination, and applying the appropriate torque when tightening bolts or crimps.
Regular inspection and maintenance are also important to identify any signs of wear, corrosion, or loose connections. This can be accomplished through visual inspections, electrical resistance measurements, and infrared thermography. Additionally, periodic tightening of bolts or crimps may be necessary to maintain secure connections.
It is recommended to have a qualified electrician or technician perform the installation and maintenance of 250 MCM lugs. They can ensure that the work is done correctly and safely, minimizing the risk of electrical hazards or equipment damage.
Conclusion
250 MCM Wire Lugs are indispensable components in renewable energy projects, providing the necessary capacity to handle the high currents generated by solar farms, wind power plants, and battery energy storage systems. By understanding the factors involved in selecting, installing, and maintaining these lugs, project owners and engineers can ensure the efficient and reliable operation of their renewable energy infrastructure.